SKELLET Upper-body Motorized Exo-skeleton
Expertly spearheaded the project management, design, manufacturing, testing, and optimization of a complex motorized exoskeleton to capacitate the user with augmented physical strength and mobility. Consistent analysis, inspection, and documentation through project milestones was of high priority. The project was able to increase "strength" by 15 pounds or allow the use to maintain a raised arm position without having the user produce any force. Achieved recognition as most valuable team member and leader, as consequence, elaborated suggestions to improve the efficiency of this program for future student generations. This action was appreciated by lead professors of this program.
This project was created with the following software and tools:
Solidworks
Arudino with Arudino Programmer
NYU’s Clocktower Prototyping and Manufacturing Lab
Makerbot 2 and 3 3D Printers
Stratasys Elite 3D Printer
Final Phase
Final version successfully completed the objective of alleviating 15 pounds of weight via the arm on the user. The final version uses a mechanical system of two high torque DC motors, metal wire, and pulleys across the 2 points of rotation along the user’s right arm. In the future if more time and money was available we would aim to further reduce weight by removing excess material, increase ergonomics/comfort for a larger set of users, use stronger DC motors that could rotate faster, and implement a sensor system for more dynamic movements.
Final Solidworks 3D Model
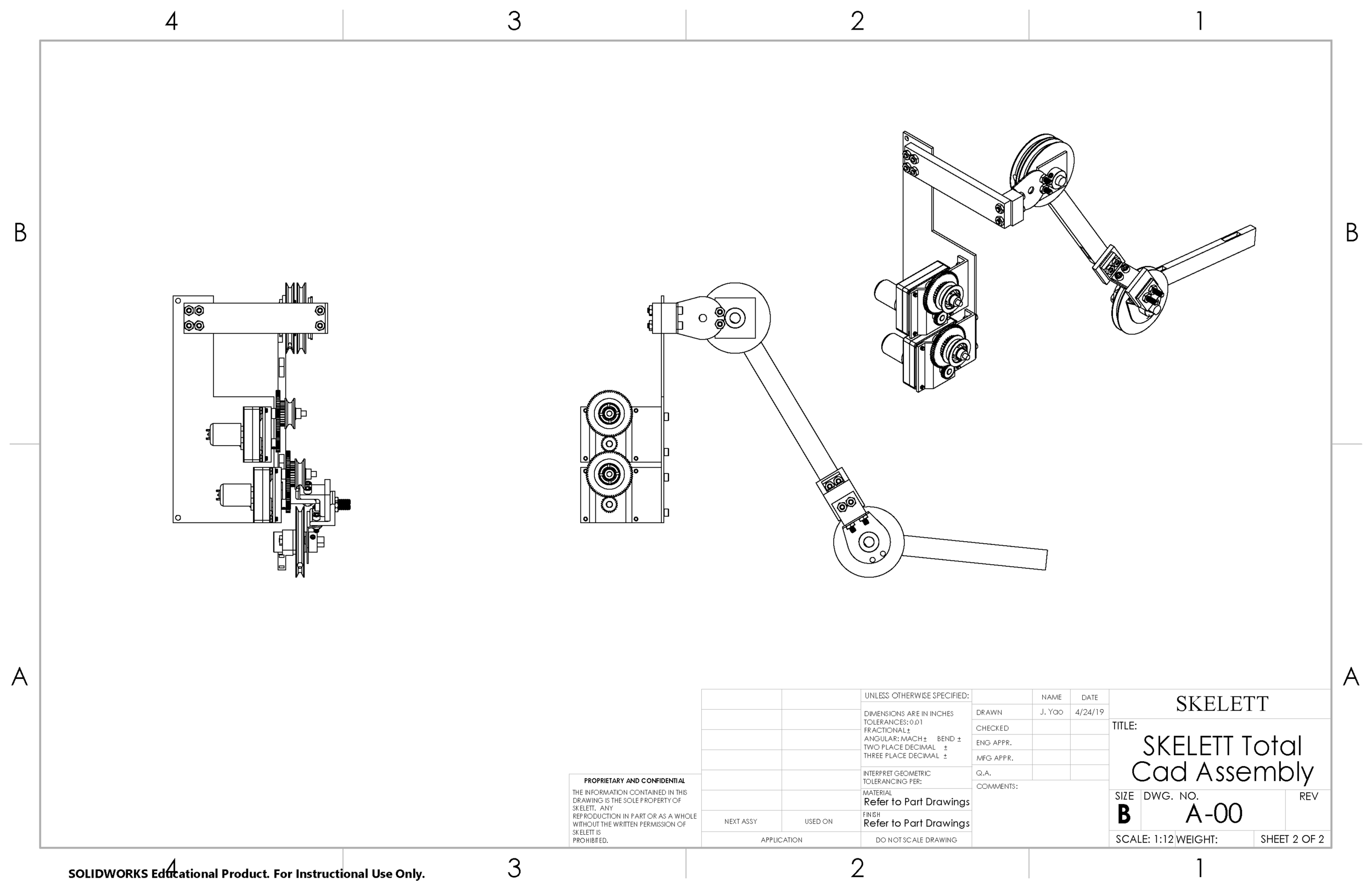
Final Prototype
Secondary Design Prototype Phase
Initial 3D printed prototype of the newly redeveloped design that proved design concept and range of motion.
Initial Design and Research Phase
The initial design of the project envisioned to complete the same final objective, however, aimed to be as compatible with as many people as possible by being able to change length to adjust to different people’s arms. Due to time restrictions the project was simplified to fit the mean length of two people’s arms on the team. In addition, weight and material was substantially cut down in order to reduce load on the user and motors.